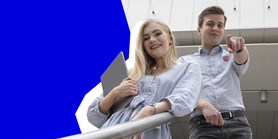
Investigation of ionized metal flux fraction at industrial conditions
Autoři | |
---|---|
Rok publikování | 2023 |
Druh | Konferenční abstrakty |
Fakulta / Pracoviště MU | |
Citace | VAŠINA, Petr, Jaroslav HNILICA, Peter KLEIN, Stanislava DEBNÁROVÁ, V SOCHORA, Martin UČÍK, Jan KLUSOŇ, Mojmír JÍLEK a A LÜMKEMANN. Investigation of ionized metal flux fraction at industrial conditions. In International Conference on Reactive Sputter Deposition 2023. 2023. |
Popis | The objective of this study is to present two distinct strategies for enhancing Ionized Metal Flux Fractions (IMFF) in industrial settings, particularly aiming to achieve values close to 40 percent for Titanium (Ti) sputtering. Additionally, we aim to demonstrate the impact of IMFF enhancement on the quality of deposited layers in both non-reactive and reactive processes. In the first strategy, we conducted experiments in an industrial setting utilizing a deposition system developed by SHM (Sumperk, Czech Republic). This system featured a titanium cylindrical rotating target with a racetrack area of approximately 100 cm2. An efficient target cooling system enabled us to deliver up to 35 kW of DC power to the central sputtering cathode, resulting in an exceptionally high ionized metal flux fraction of 23 percent at the substrate level. This value is notably close to what is typically achieved with high-power impulse magnetron sputtering (HiPIMS) technology. The measurement of this high value challenges the commonly accepted notion that IMFF in DC magnetron sputtering is typically only a few percent at the substrate level. This exceptional result is attributed to the equipment's technical advantages, allowing for extremely high-power density. Additionally, we demonstrate the potential to increase IMFF by up to 10 percent using a hybrid deposition system that combines lateral glow discharge with magnetron sputtering. This hybrid technology offers independent control over the ion and neutral fluxes on the substrate, resulting in a pronounced preferential 111 orientation of TiN grains and improved hardness and roughness of TiN coatings compared to standard magnetron sputtering. The second strategy was implemented in an industrial setting using a deposition system developed by Platit (Platit AG, Salzach, Switzerland and Platit a.s. Sumperk, Czech Republic). Platit introduced a novel cathode, referred to and marketed as the "F-type cathode," which optimally concentrates the total power into a small target area while actively preventing overheating. This approach enables the attainment of high-power density, reaching up to 400 W/cm2 in the racetrack region, leading to IMFF values of up to 35 percent. It's important to note that the F-type technology employs standard DC sources but achieves results as HiPIMS. The primary distinction lies in the concentration of power in a small area but continuously delivered for F-type cathode, as opposed to HiPIMS, where power is delivered across the entire target area but in short intervals. Coatings deposited with the F-type cathode exhibit density and smoothness comparable to HiPIMS layers. In summary, this study explores two innovative strategies for increasing IMFF in industrial settings, shedding light on their potential for enhancing the quality of deposited layers, as was already demonstrated for reactive and non-reactive sputtering of titanium. |